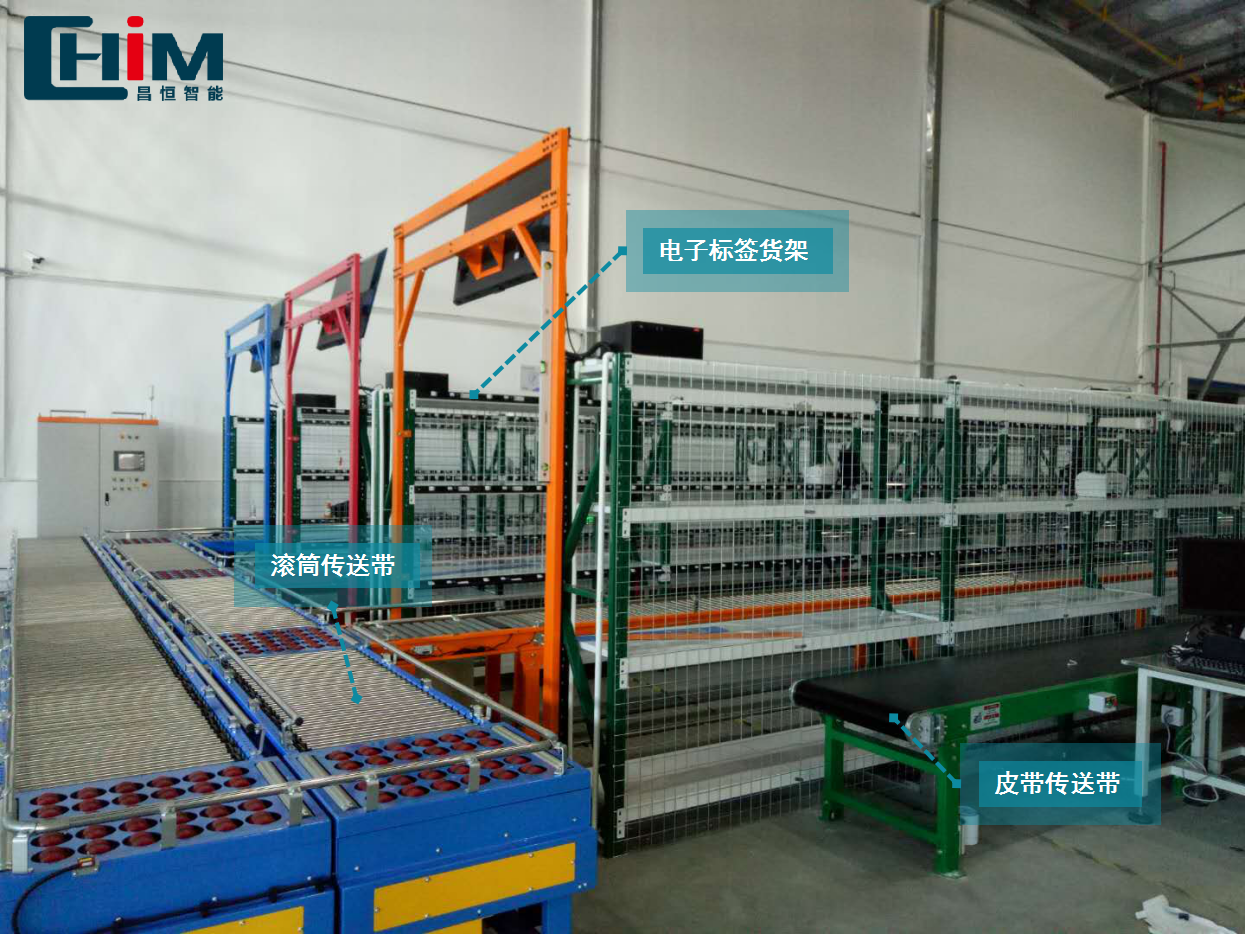
Descripción general del proyecto
Changheng Inteligente estableció una solución automatizada de clasificación de pedidos para Starbucks' RDC (Centro Regional de Distribución) en una ciudad china.
Este sistema automatizado de picking de almacén está diseñado para:
â Manejar las demandas de pedidos de alta frecuencia de 90 tiendas
â Garantizar la precisión de la clasificación al tiempo que mejora la velocidad para mantener la frescura de los ingredientes
Arquitectura del sistema
- 3 líneas de producción con transportadores de rodillos
- 1 línea de producción con 8 estantes de etiquetas electrónicas
- Transportador de rodillos trasero para la transferencia automática de cajas
- Cinta transportadora en el lado derecho
Proceso Operacional
Los empleados realizan la selección de piezas guiados por Indicadores luminosos en estanterías de etiquetas electrónicas. Los pedidos son descompuestos por el sistema informático y transmitidos a las ubicaciones de almacenamiento correspondientes.
Tres líneas de producción se conectan al transportador de rodillos trasero a través de Clasificadores de bandeja basculante de 90°con Sensores instalados cada 500 mm para la alineación automatizada de cajas.
Ventajas del proyecto
- Experiencia en estanterías de etiquetas electrónicas y automatización de almacenes
- El diseño modular minimiza el espacio ocupado por el equipo, maximizando la capacidad de almacenamiento
- Soluciones rentables y fiables adaptadas a escenarios operativos
Beneficios para el cliente
â Visualización de pedidos en tiempo real y seguimiento de la cantidad de salida
â La codificación cénica permite la gestionón de lotes y fechas de caducidad
â La selección guiada por luz a prueba de errores mejora la precisión
â Reducción de los costos de mano de obra y el esfuerzo físico a través de la automatización